Camada Daybed

The prototype Camada daybed designed by Ash Fischer and Orlando Hayes proved that furniture made with 100% recycled plastic and upholstered in Australian wool can be beautiful, eminently collectable and valuable. A big question put to the pair during the six-month Carl Nielsen Design Accelerator program was whether they wanted to continue as designer/makers or explore a new path to commercial success. Fischer and Hayes share their big realisations in this interview recorded by Powerhouse editor Stuart Ridley just before they presented the daybed at the International Contemporary Furniture Fair in New York in May 2024.
‘Changing from a designer/maker just to being a designer was probably one of the biggest decisions.’
Ash Fischer Our main goal was to establish a refined product everyone’s happy with and I think that’s stayed true. This industry is pretty hard to get your foot in the door unless you have some sort of some financial backing, so getting funding behind a project helps a tonne. And having access to Adam Goodrum as the program mentor has been incredibly valuable, along with help from people at Powerhouse like Angelique Hutchison (Collection Curatorial), Tane Andrews (Exhibitions) and Tashi Grey (Program Curatorial).
I remember studying Adam Goodrum at uni and then having meetings with him every fortnight for this project was pretty surreal. Going through the program we realised how not ready the first prototype was and how far away we were from reaching a market that can purchase a daybed of this value. So it definitely changed from thinking we knew what to do to really quickly realising we had no idea.
Orlando Hayes Adam knows the industry so well and helped us through the chaos when trying to navigate a pretty mysterious sector. We had just finished our first prototype type daybed and we were like, ‘Yeah, it's great. It's good to go’, and we were pretty keen to just launch it and get help for it. We really wanted to sell at least one. Adam also connected us with Kvadrat Maharam, which is an internationally renowned upholstery fabric company we are now using for the daybed. He also put us on to Jay, who runs Demuz, which is an upholstery business in Western Sydney. He’s an absolute gun at upholstery prototyping and design upholstery and difficult projects.
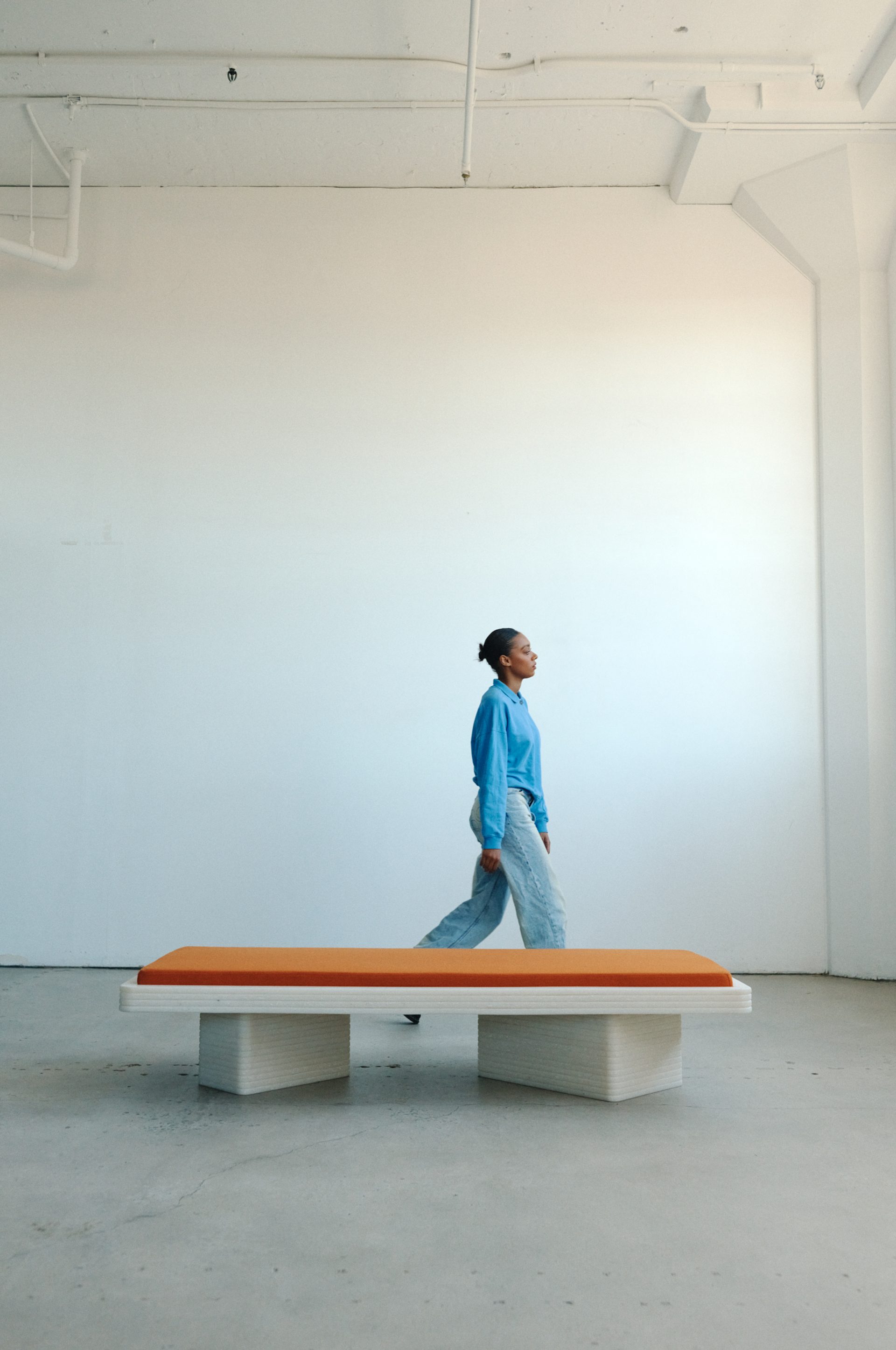
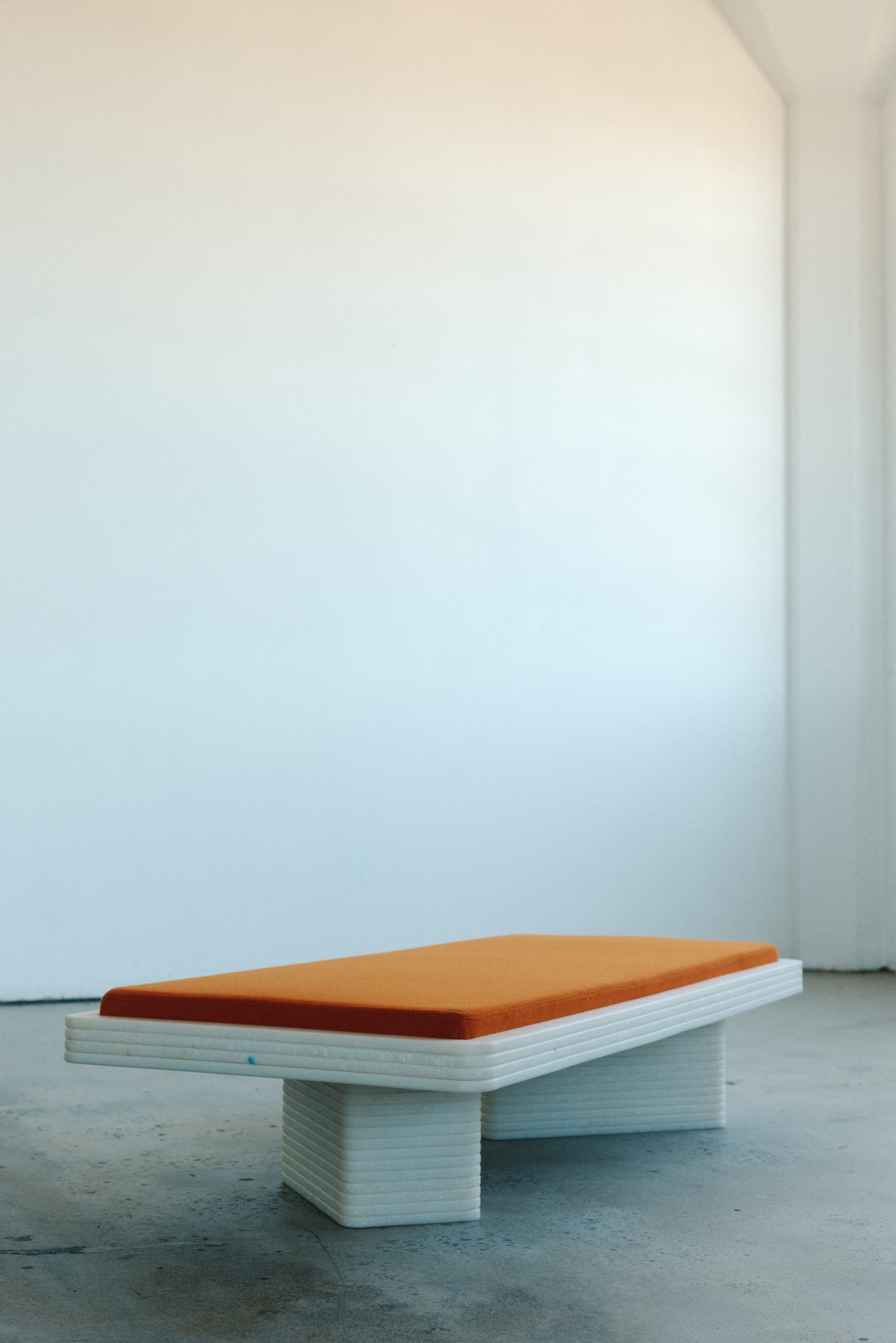
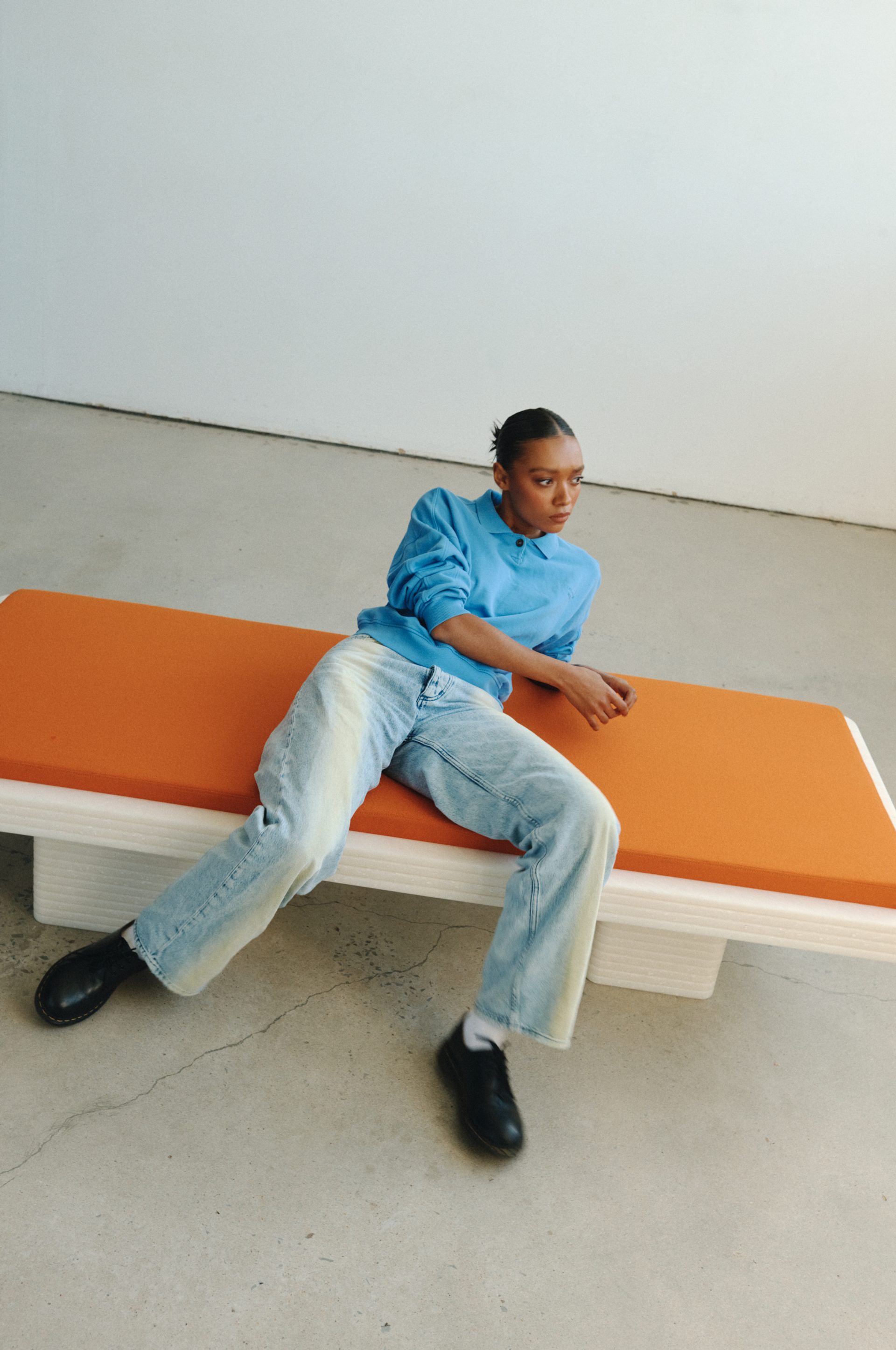
Career Focus
AF I think especially for young people getting into a creative industry like design, support is really needed because as we've found out through this program it’s a pretty brutal industry.
We had an interview with Nick Karlovasitis, founder of DesignByThem, and he pretty much put it straight forward to us. He's like, ‘Do you want to be designers or manufacturers?’ Which is a great question that took us both a while to think on.
Changing from a designer/maker just to being a designer was probably one of the biggest decisions. When you're at such a small level in the design world to get the connections to make a sellable high-end piece is really hard. The first one weighed at least 150 kilos, and during the program we brought that down to about 80kg, which is insane. The guys at Defy (recycled plastic design studio and manufacturer) helped us do that, showing us how we can engineer it better by changing some aspects of the design.
Lessons in Manufacturing
OH One of the hardest things in manufacturing the first daybed was we spent 16 collective hours sanding and three hours assembly. It was a really fun process, but we had to make it scalable to make it commercially viable. Just figuring out, okay we made one, now how do we make ten, 20 or 100? How much will it cost and who is going to manufacture them? Working with the people at Defy we made it more of a standardised, repeatable process. We worked with Defy to refine the pinning system, which requires really tiny tolerances between that pin and the main piece of plastic, and made that tolerance enough to hold the daybed together, but also easy enough to assemble so you don't have to like mallet it in all the time and near break a daybed each time.
We also learned a lot about the CNCing process [a Computer Numerical Control machine using a computer to control tools in manufacturing processes] and how to bring down our wastage of materials. I think when we started it was like 60% of the material was used to about 80% now.
And then for sanding, we’d been a bit gung ho the first time and sanded every surface but now we’re focusing on the exterior of the piece, just what we have to do, as opposed to trying to do it all.
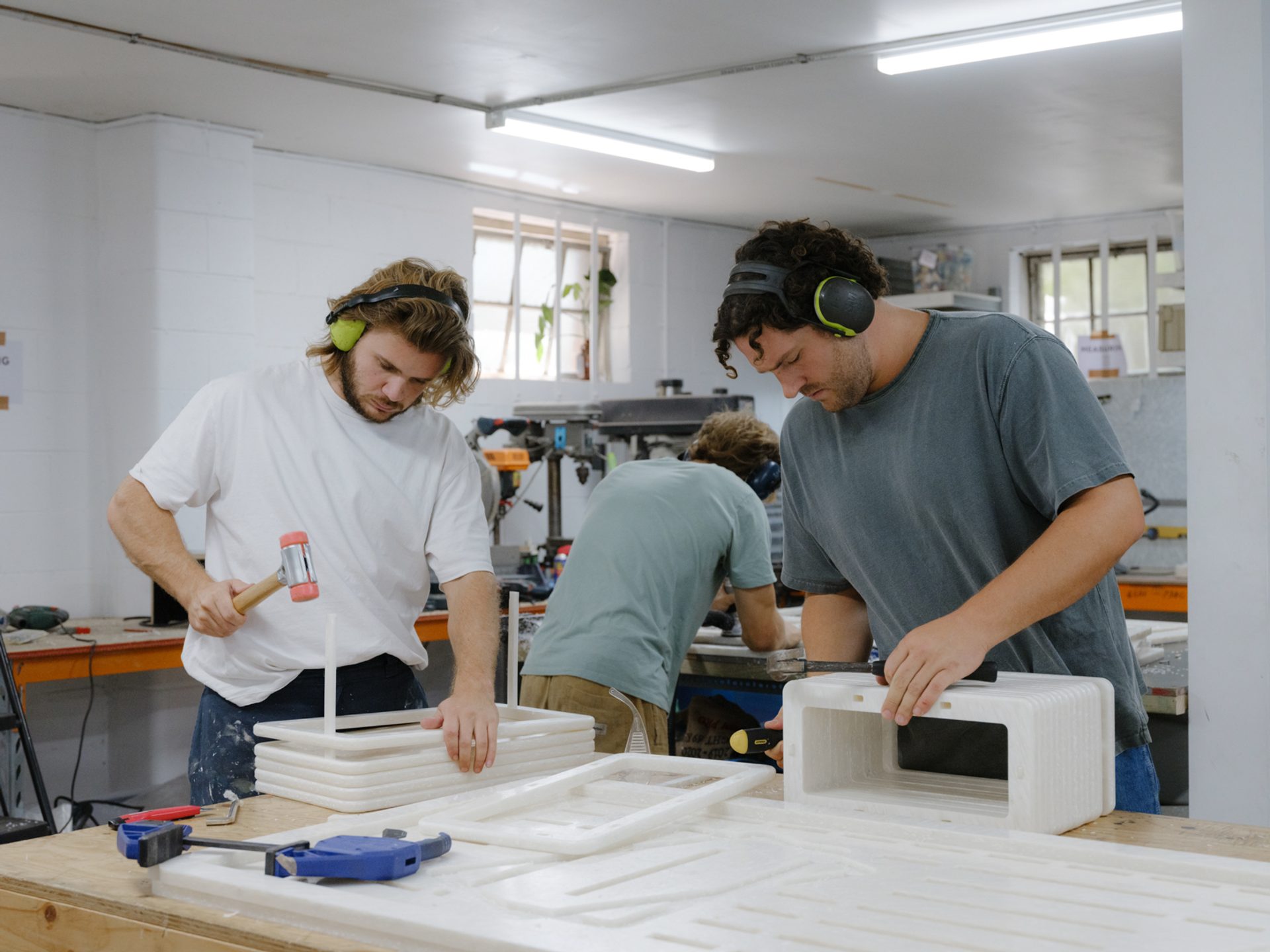
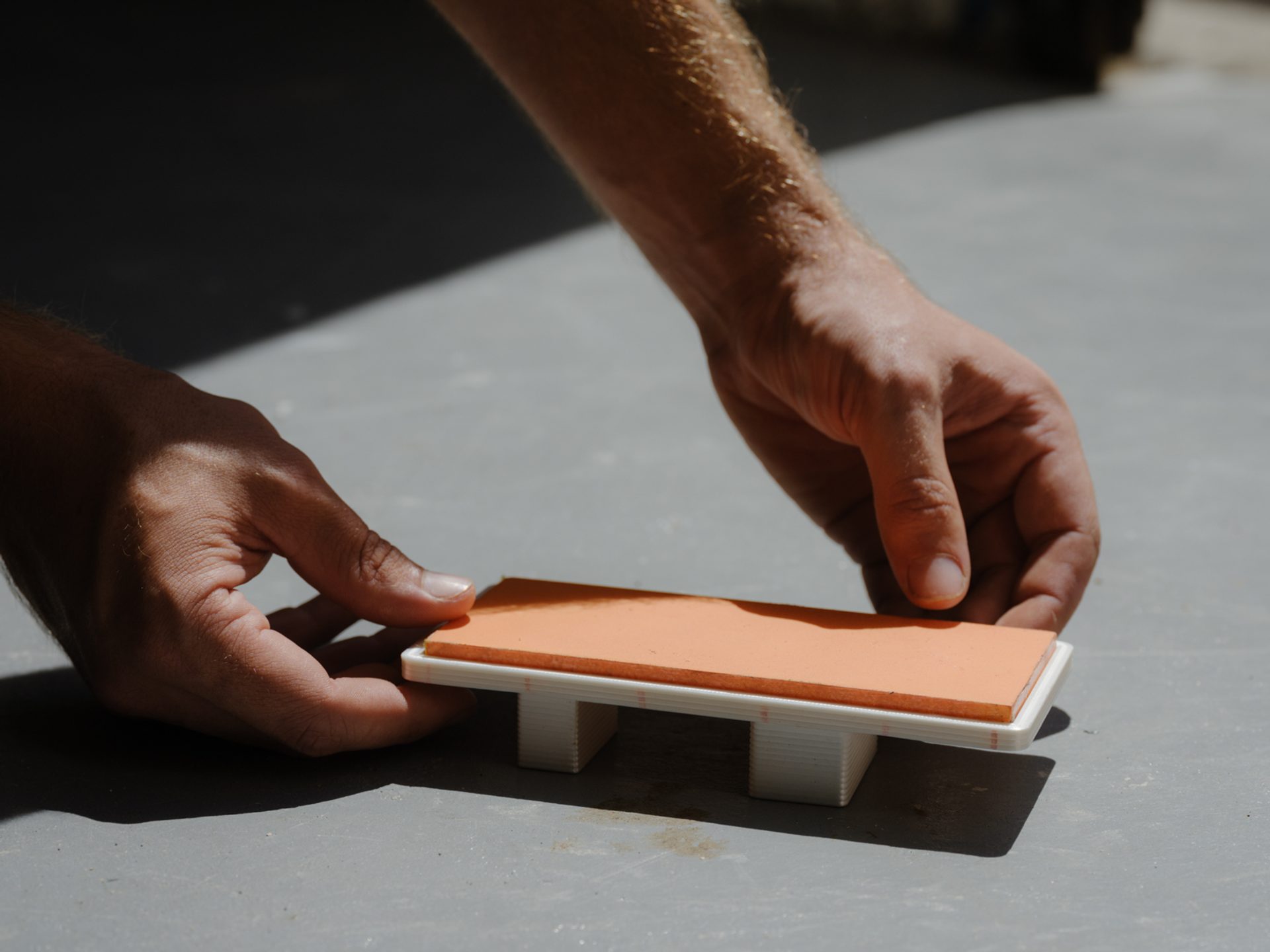
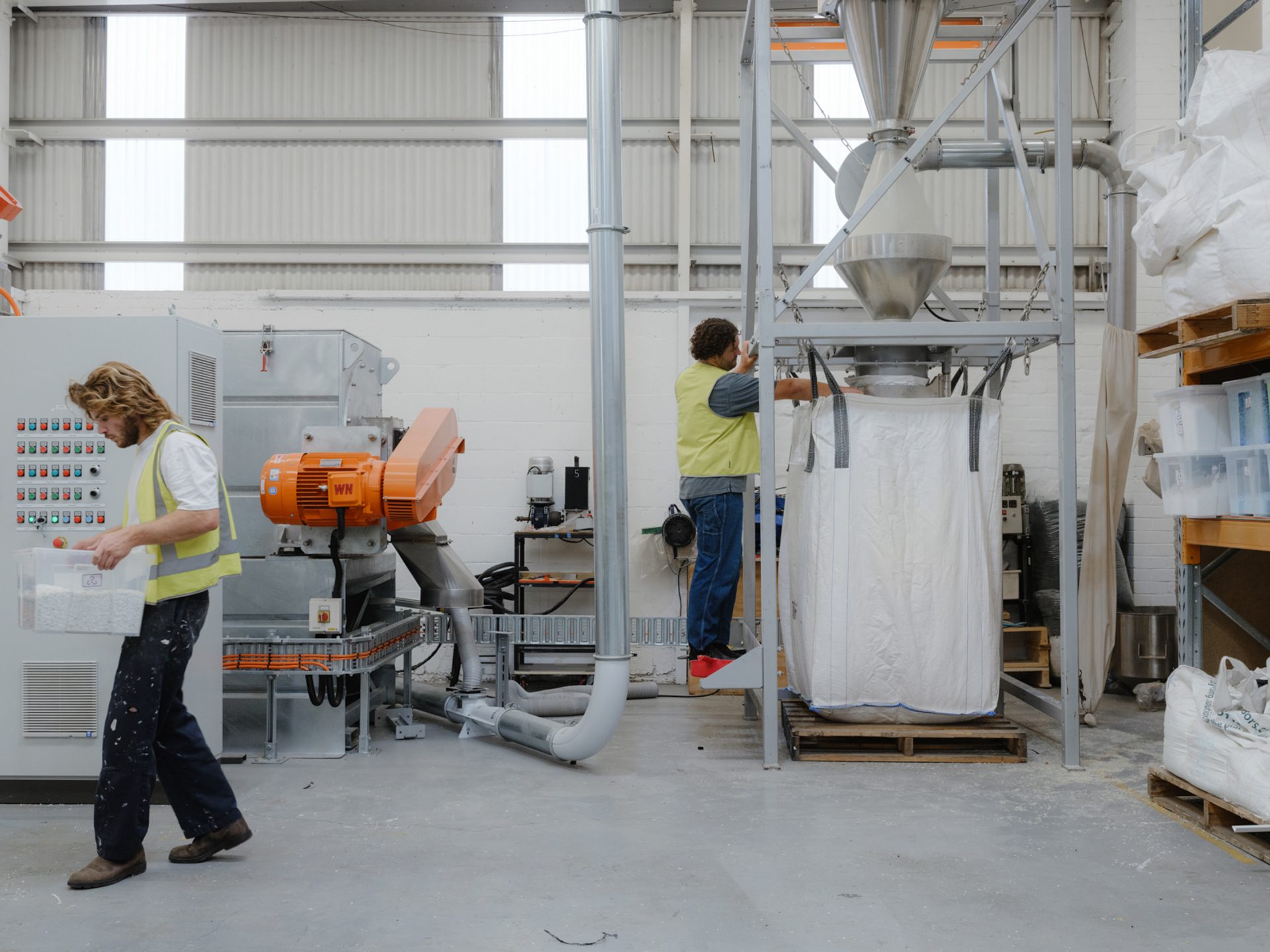
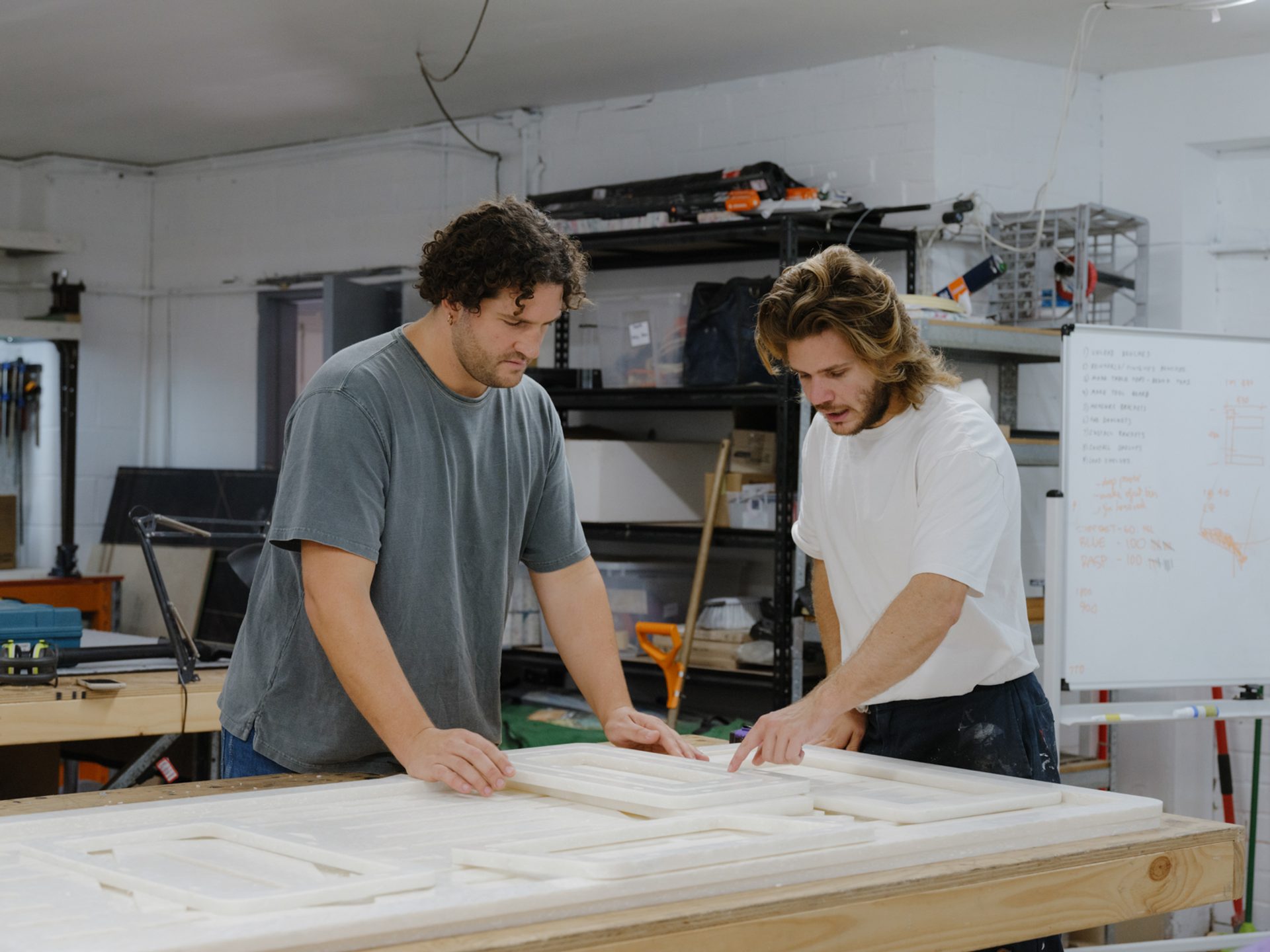
Sustainability Improvements
AF The first daybed used more recycled materials, so that has benefits as well, but there was more waste because we weren’t seeing how it would be laid out on the CNC. The benefit with the recycled plastic is any waste can be reused.
I guess there's no such thing a complete zero waste product, but the frame of the bed is up there. Now we’ve changed what we get out of each sheet, from three and a half sheets to two.
OH What we’re trying to do in making such a big piece is to take as much of that plastic as possible from a wider recycling system and make a statement about it as a more high end material. We want to put it in people’s minds it does have the same level of value as say pure resin or raw virgin aluminium. So it’s the idea of capturing those materials, locking them up in heirloom pieces that are going to last a lot longer and hold a lot more value.
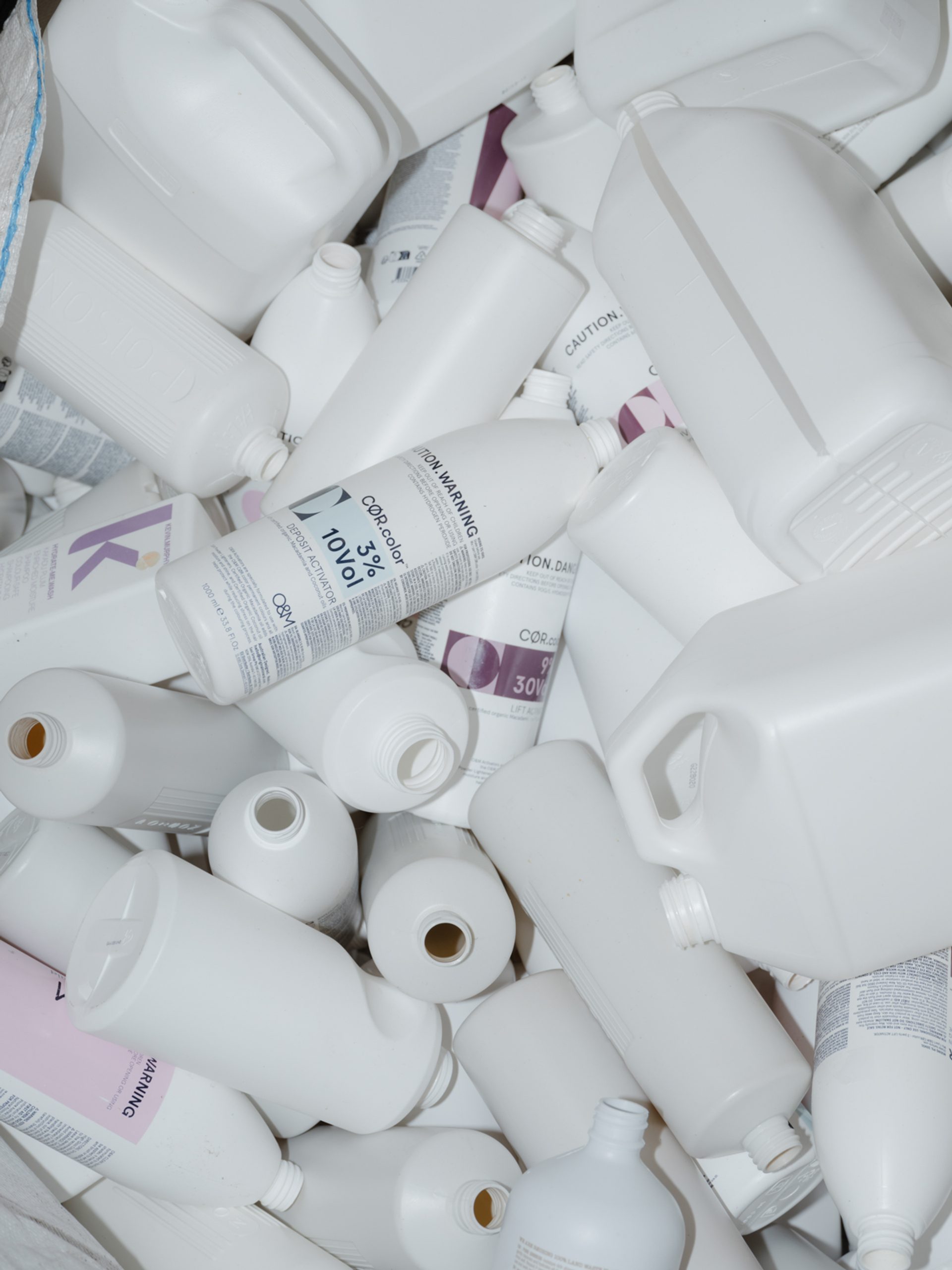
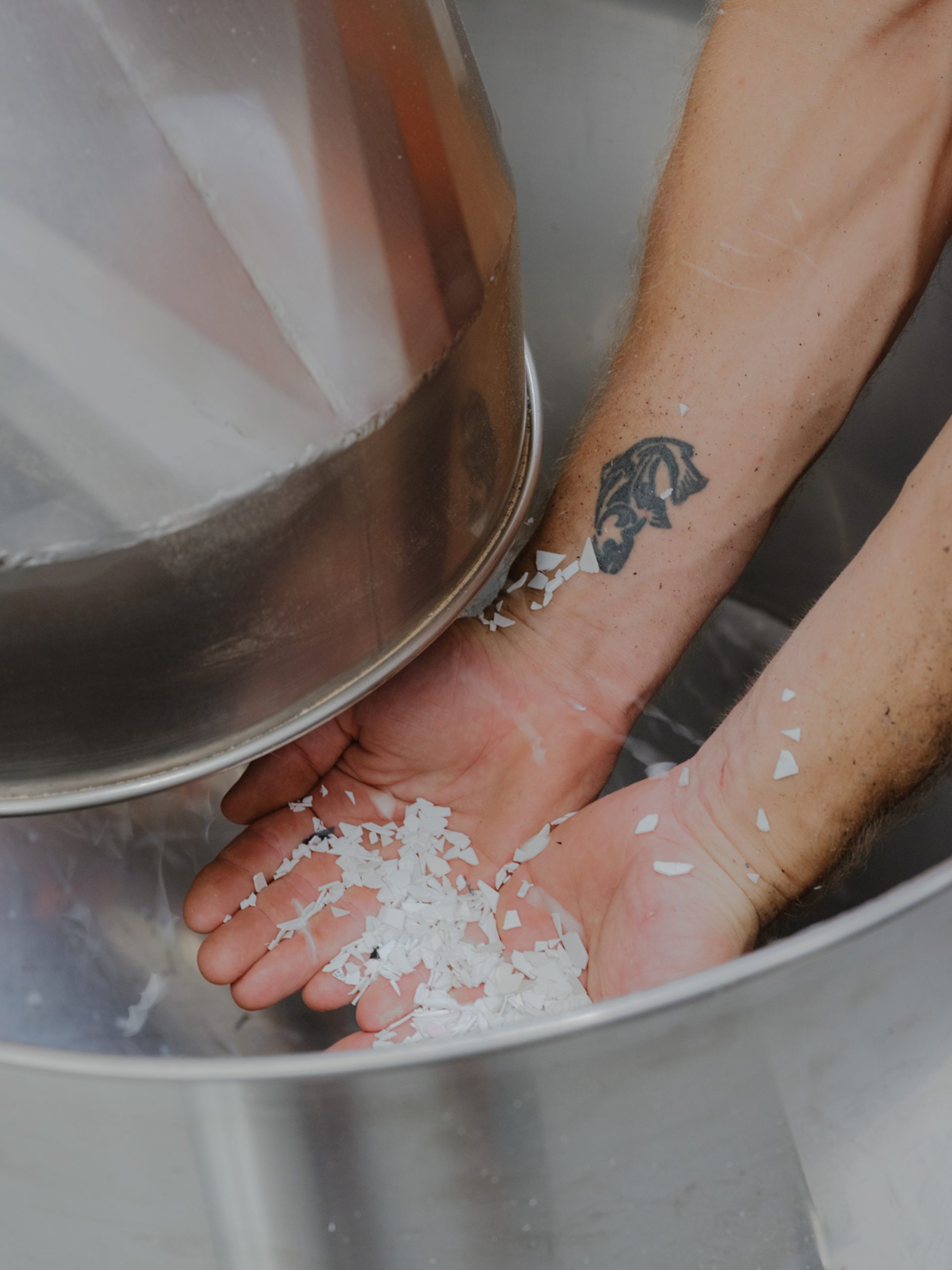
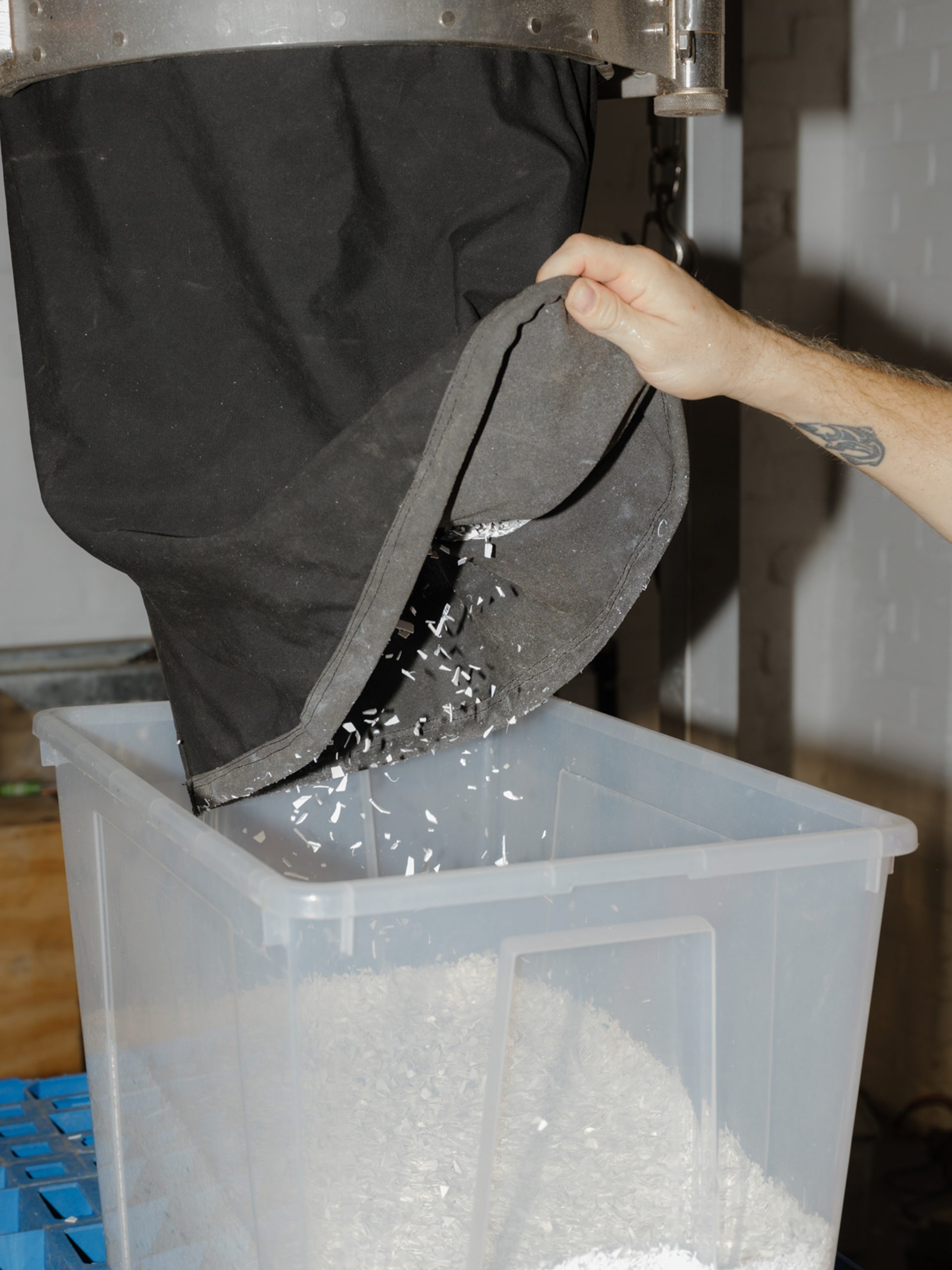
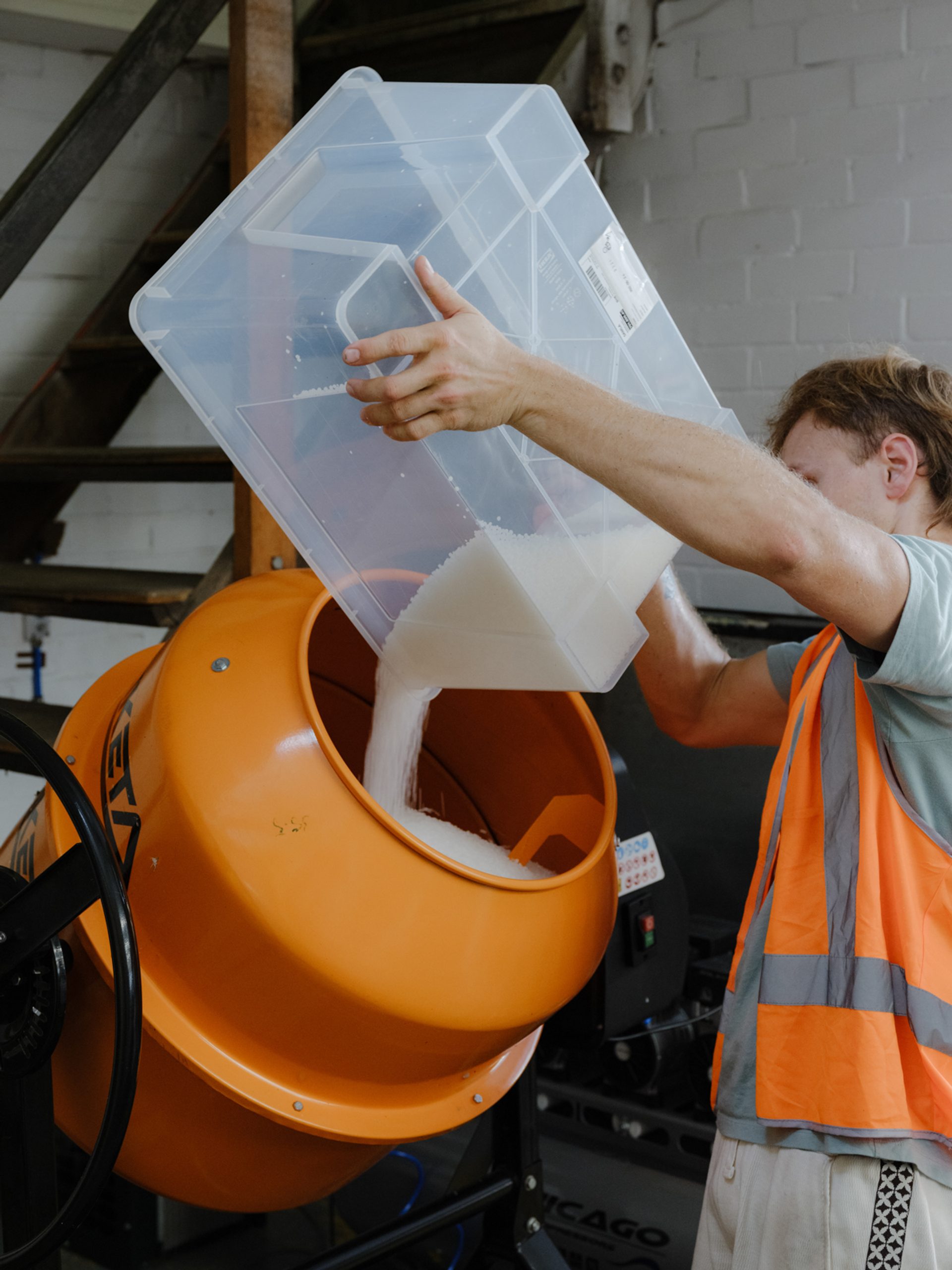
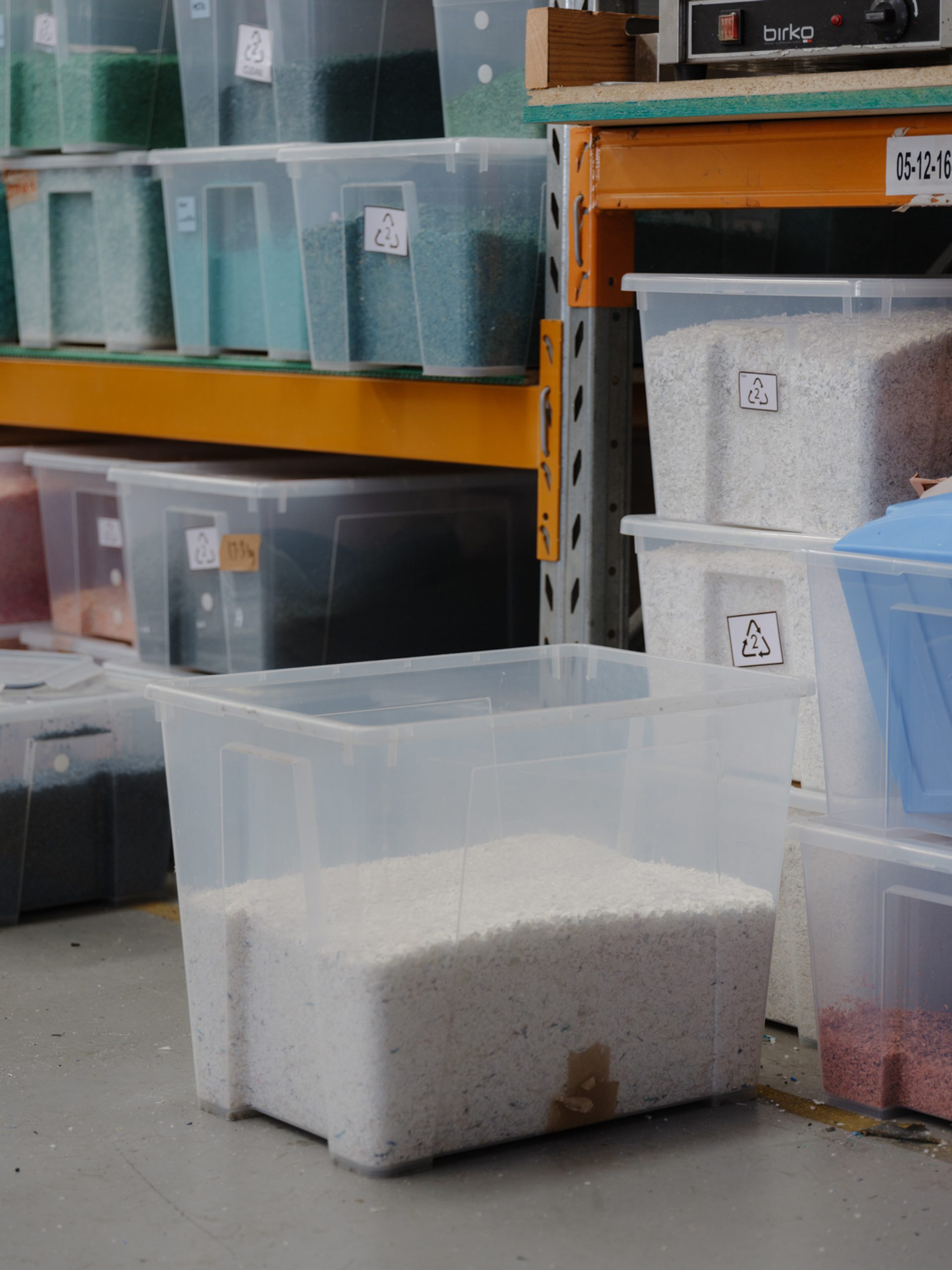
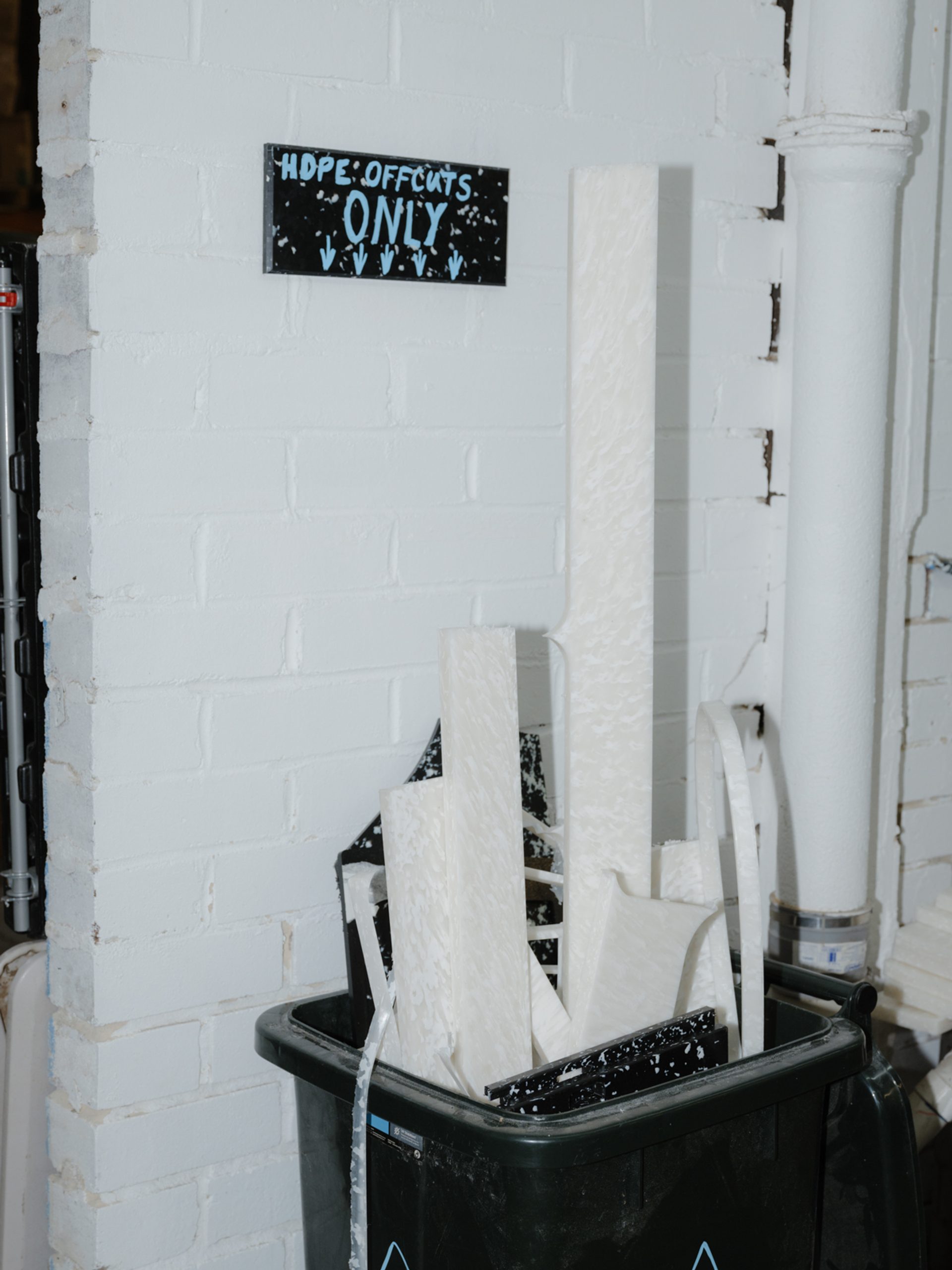
Seedling Ideas
AF If you’ve read Rick Rubin, the music wizard, he has this thing called seedling ideas, which we’ve adopted. Basically we have ideas that are actually being made like the daybed, and then we have three whiteboards in our workshop and a big table filled with lots of scribbles of seedling ideas.
‘Camada’ means layer in Portuguese and because of the stacking system being such a simple effective and aesthetically pleasing process, we would like to do a series. So we're looking at doing stools, a table and potentially a bed frame. So we’re going down a plastic avenue for a bit. I think the big benefit of choosing to be a designer instead of a designer/maker is the freedom you have to not stay in one design for too long.
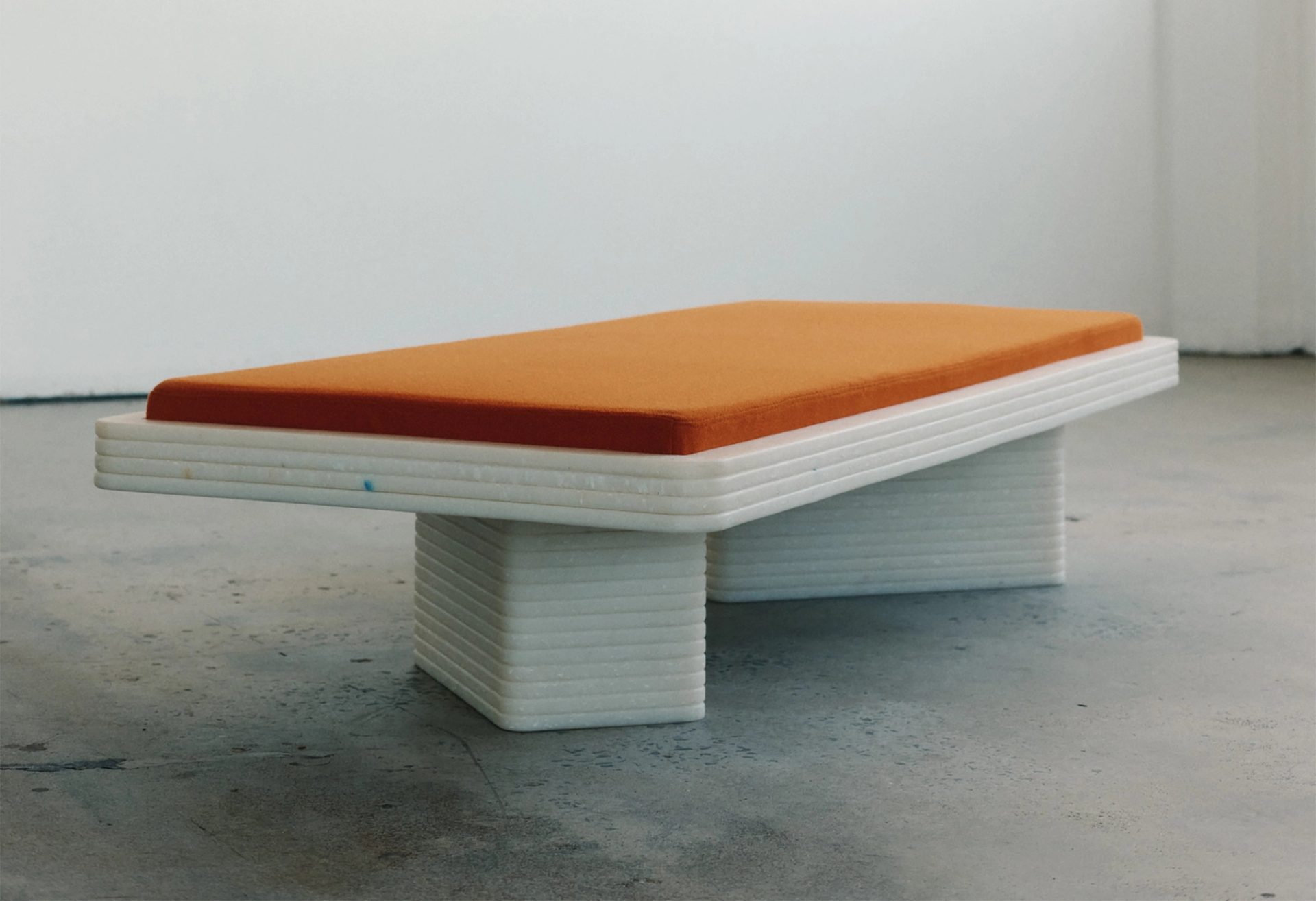
International Opportunities
AF So we're going to New York in two weeks with the daybed and I think after that it will feel really cemented. We’re still quite small but it shows we’re worth the recognition.
A mentor of mine in Melbourne suggested we enter the daybed in the International Contemporary Furniture Fair, which is happening in Manhattan. We submitted the design a week before submissions closed and we got in.
So apart from very much enjoying the process, we also have this time frame on the daybed. We have a manufacturer in the US making one now and while it’s all very down to the wire and stressful it’s very exciting at the same time.
OH We’re making a daybed over in the US so we can minimise international shipping. We've met with a recycling place over there that does recycled high impact polystyrene, and they’ll be making us a custom US version of the daybed, which keeps that recycled material there. So that idea of locking it up in this design we can distribute and sell in the US.
We’re also part of the Lumens at ICF, which is a ‘Best of’ feature of the top 18 participants in the ICF Wanted list. It’s a public choice program, so we’d love for people to vote for us.
Carl Nielsen Design Accelerator
An annual initiative recognising achievement by Australian industrial designers working in sustainable design.
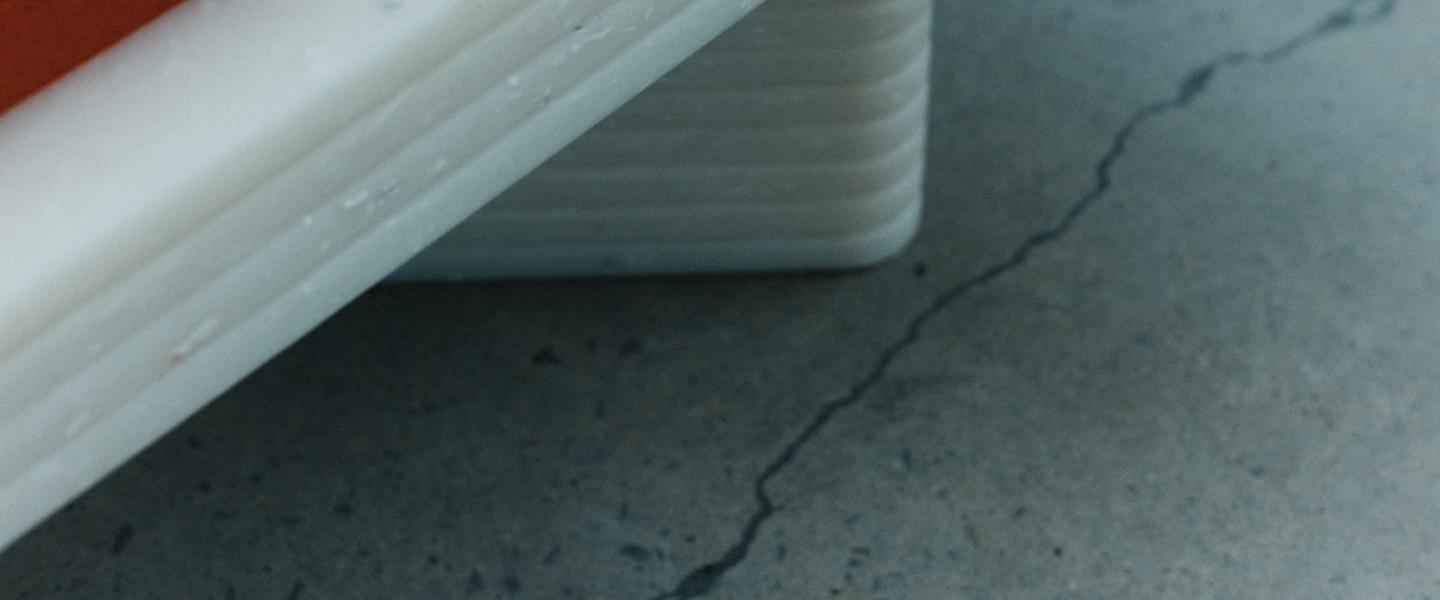
The annual Carl Nielsen Design Accelerator, supported by a generous bequest from Carl and Judy Nielsen, recognises achievement by Australian industrial designers working in sustainable design. Powerhouse will select one project designed in Australia that demonstrates outstanding design for sustainability.
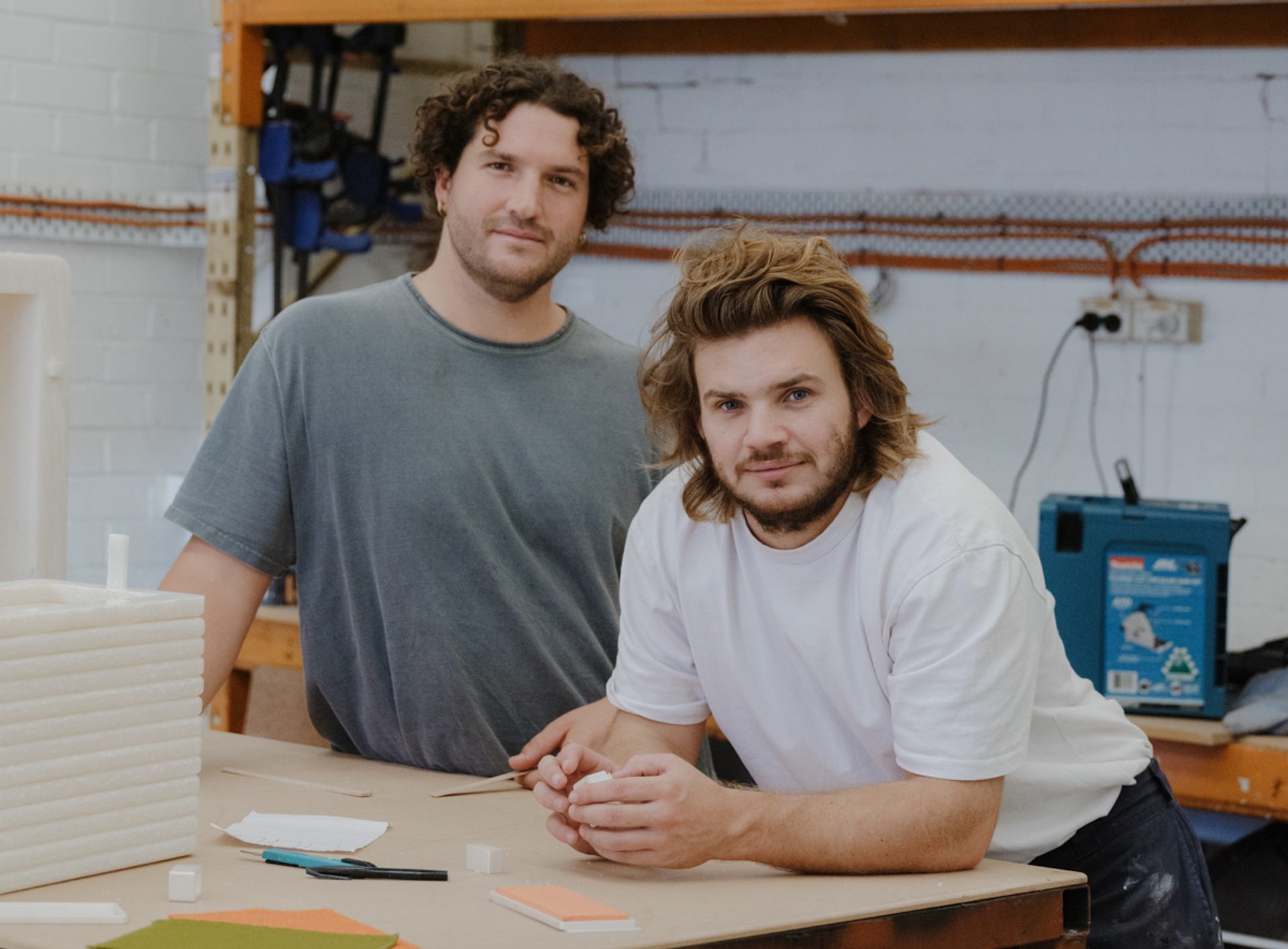
2023 Recipients
Ash Fischer is an emerging designer from Sydney Australia with a design incentive focused on sustainability. Since establishing Fisch Designs in 2020 he has built up a portfolio of six designs ranging from an ashtray to a daybed. With distinctive motifs of colour, materials and shapes, his designs have sold globally and one of his works, the Lucha Floor Lamp, was acquired by the National Gallery of Victoria after it was presented at the 2022 Melbourne Design Fair. Ash Fischer’s style is a modern take on retro futurism, reviving the once giddy optimism of people’s predictions of the future through design.
Orlando Hayes works on expanding approaches to design in collaboration with local ecologies and global environmental systems. After completing a degree in Environmental Science at UNSW, he began his career working in sustainable design of urban infrastructure at Arup, followed by a stint with Australia’s first dedicated regenerative design team led by biophilic architect Amanda Sturgeon. Hayes is currently working with CH4 Global to lay the foundations of sustainability for the organisation as it develops solutions to reduce enteric methane emissions from cattle. As he continues to collaborate with designers, artists and organisations, Hayes looks to distil emerging environmental principles and ideologies into new design ideas and practices.
Community
New work across the applied arts and sciences is developed through support and investment by Powerhouse. We foster innovation through facilitating collaboration and connection between industry and community.